Two Spindle Screw Pump ( Series D2S)
Delta Twin Screw pumps work on unique principle that makes it the only choice for certain applications. No other design of Positive Displacement Rotary pumps offer so much versatility in the operating parameters with guaranteed total reliability and maintenance-free service.
Major Industries Petroleum refineries, Terminals, Depots, Oil blending stations, Thermal power plants, Steel plants, Fertilizer industries, Petrochemical plants, Carbon black, Sugar, Paper and Pulp, Marine.
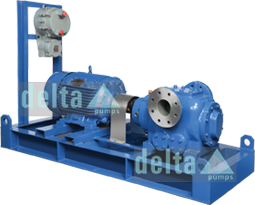
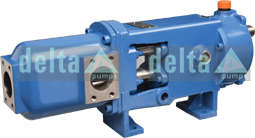
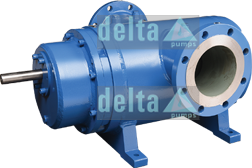
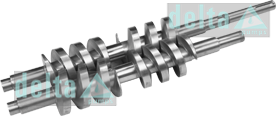
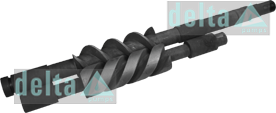
Working Principle:
- A pair of specially profiled screw, machined integral from solid stock and well supported on antifriction bearings run in precision bored interchangeable casing liners. Each screw set has one right hand and one left hand screw engaging with a similar but opposite hand screw pair.
- A pair of hardened and profile ground timing gears synchronize the screws to maintain a small but positive clearance between the flanks thus ensuring no metal to metal contact. The pumps can therefore run dry for sometime without any damage. This unique feature enables to run the pump even dry and handle fluids that do not have enough lubricating value and also very low or high viscous products.
- Consequently, since there is no metal to metal contact; wear and tear is reduced to the minimum, ensuring extremely long service life. With two pairs of screws running in the same casing, the internal velocities are very small - consequently the NPSHR is practically the lowest even when the pumps run at motor speeds and while handling viscous products. Opposed screw pitches totally eliminate axial thrusts. Relatively small diameters of screws enables the pump to operate at high speeds directly coupled to prime movers - without the need for speed reducers even while handling high sealing’s always under suction pressure, thus making use of simple, inexpensive seals.
- The axial flow without turbulence, rotation, churning, chewing guarantees gentle handling of products. Noise and vibration or ---- levels are about the lowest. Positive clearance between running parts makes it easier to construct the pump in different materials safely, especially in stainless steel, without the fear of seizing. Thus a variety of fluids can easily be handled by selecting the right materials of construction.
Salient Features:
- Positive clearance between rotors
- No metal to metal contact between rotors
- Dry running capability
- Axial smooth steady flow
- High speed running
- Pulsation free output
- Negligible vibrations
- Insensitive to varying viscosities
- Long maintenance free service
- Lowest NPSHR
- Negligible wear over years Shaft sealing at suction pressures
- Axial thrusts completely eliminated
- Interchangeable liner
- Adaptability of various MOC
Typical Parameters
- Typical Parameters
- Temperature: -30 to +350°C
- Viscosity: 1 cSt to 50,000 cSt or more
- Capacity: 20 to 500 m3/hr
- Pressure: Normal 16 bar/ 24bar, with special designs up to 50 bar
- Specialties: Partial heating/ complete heating/ cooling arrangements
- Sealing: Stuffing box/ mechanical seal with or without quenching/ heating/ cooling
- Mounting: Horizontal foot mount/ vertical pedestal
- Accessories: Relief valves, base frame, coupling, coupling guard, companion flanges, pressure gauges, electric motor/ diesel engines, variable speed drives and as per customer requirements.
Typical Applications
- Typical Applications
- Loading / unloading of fuel oil and other products from: Railway wagon rakes, Truck tankers, Barges, Ships and Tankers.
- Bulk cargo handling.
- Lubrication, circulation and cooling.
- Process pumping of high viscous products, bitumen, molasses, soap and similar products.
- Long distance pipeline pumping of viscous products.